The overall structure of a car is basically made up of four parts: the engine, chassis, body and electrical appliances. Automobile engine is the engine that provides power for the automobile, it is the heart of the car. Other parts also play irreplaceable role in automobile applications. Let's understand the grinding involved in the processing of these four components and the grinding products and services we can provide.
What superabrasive tools will be used for processing auto parts?
Here, you will find the answer.
Engine
Engine is a complex machine built to convert heat from burning gas into the force that turns the road wheels. These engine are named heates. There are many kind of engines like electric motors, pneumatic motors and other. This article is about internal combustion engine construction. Internal combustion engine consists of next main parts: crank-mechanism, valve operating mechanism, cooling system, lubrication system, fuel system, ignition system and starting system.
Crankshaft-mechanism
A type of innovation with the grinding wheels, the crankshaft grinding wheels finds its usage in the different automotive, truck, diesel, aircraft, and small engine manufacturing industry and also in the various engine rebuilding firms that are used to regrind the pins and the bearings.
1. Main Bearing and Crankpin Journals Grinding with Vitrified CBN Wheels
Cubic boron nitride (CBN) grinding wheels are used for high production machining of automobile crankshafts
Applied material
Cast iron: chilled cast iron, nodular cast iron, grey cast iron, alloy cast iron, etc
Steel: 20Cr, GCr15, CF53, 45# steel, 55# steel, 80B high carbon steel, etc
Benefits
- Long dressing interval = Long tool life
- Consistent surface finish and high profile stability
- Reduced thermal and mechanical damage to workpiece
Crankshaft Grinding Machines
NTC, TOYODA,LANDIS, MIKROSA, JUNKER, SCHAUDT, EMAG,Etc.
2. Main Bearing Grinding with Vitrified Aluminum Oxide Wheels
When producing small lots or machining larger crankshafts (for trucks and ships), grinding wheels with aluminium oxide abrasives are used.
.png)
Benefits
-The evenness of hardness and balance performance of the wheels are 30-50% higher than that of China State Standard.
- The thickness deviation of a group of the wheels is not more than 0.2mm.
- The parallel tolerance of two ends is not more than 0.1mm.
Cubic boron nitride (CBN) grinding wheels are used for high production machining of automobile crankshafts
3. Rough Grinding Main Bearing and Crankpin with Electroplated CBN WheelS
A pin chasing process with electroplated CBN wheels is used for the roughing of the main and in particular the pin bearings of a crankshaft.
.png)
4. Finish Grinding FLANGE and POST GRINDING
Finish grinding with vitrified bonded aluminium oxide or vitrified cbn wheels. During cylindrical grinding operations for the flange and post, it is possible to use different specifications depending on the requirements of the respective contact zones.
.png)
5. Dressing and Truing of Crankshaft Grinding Wheels
The dressing and the truing of the grinding wheels: This is mainly done in order to restore the original cutting geometry and to make a final product which is flatter and round. The grinding wheels get their flatness and roundness from the dressing and truing of the grinding wheels.
6. Crankshaft Polishing Belt for Crankshaft Polisher Polishing
The grinding/polishing of the crankshaft uses a thin film backed diamond sanding belt. This material is completely flat, which ensures the accuracy of the grinding surface. Because the crankshaft needs to be polished to the R Angle, the grinding and polishing of the crankshaft requires the use of serrated polishing tape.
(1).jpg)
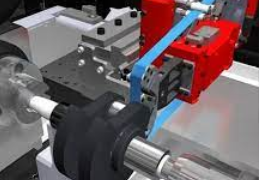
Injector Bore
The injector is a precision device with very high machining accuracy, requiring a large dynamic flow range, high resistance to clogging and contamination, and good atomization performance. The injector accepts the injection pulse signal from the ECU and precisely controls the fuel injection volume.
Grinding with Vitrified CBN Internal Grinding Wheels
Vitrified CBN internal grinding wheels are made of cubic boron nitride abrasives and sintered with metal powder, resin powder and ceramic as a bonding agent to form various shapes of abrasives for industrial grinding, polishing and lapping. This kind of Vitrified internal grinding wheel maintains the original high hardness performance of ceramic grinding wheel, low sintering temperature, high strength and toughness, good abrasive holding performance, and has the characteristics of heat resistance, oil resistance, water resistance, acid and alkali resistance, good self-sharpening, dressable and long dressing interval.
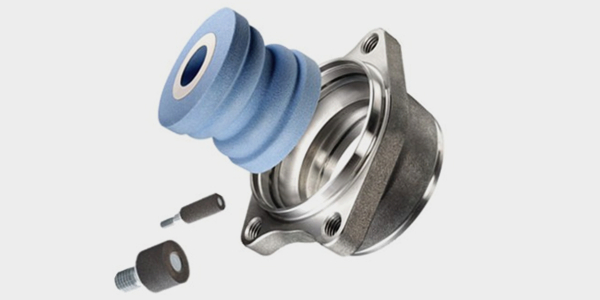
Cylinder Bore/Cylinder Block and Connecting Rod
The cylinder block is one of our engine's central components. It plays a key role in the lubrication, temperature control and stability of the engine and it has to be of the highest quality so there is no room for short cuts.
A connecting rod is the part of a piston engine which connects the piston to the crankshaft. Together with the crank, the connecting rod converts the reciprocating motion of the piston into the rotation of the crankshaft. The connecting rod is required to transmit the compressive and tensile forces from the piston. In its most common form, in an internal combustion engine, it allows pivoting on the piston end and rotation on the shaft end.The predecessor to the connecting rod is a mechanic linkage used by water mills to convert rotating motion of the water wheel into reciprocating motion.
.png)
Grinding with Metal/Vitrified Bond Diamond Honing Stone
More Superhard provide diamond and CBN honing stone for honing machines of almost all renowned honing brands (Sunnen, Nagel, Belden, AccuCut, Engis, and other types of high-production honing equipment ). Our diamond and CBN honing stones are available for precisiom bore finishing.
.png)
Engine Valves and Injection Nozzles
Directly secured to the engine cylinder head, the injector introduces fuel into the engine in the best form for optimum combustion. This requires the breaking down of fuel into tiny droplets, ranging in size from twenty to one hundred microns diameter, and spreading the droplets evenly through the combustion chamber. The injector consists of the nozzle-holder and the nozzle, with the nozzle having to close rapidly at the end of the injection in order to prevent the combustion gases forcing their way up into the injector.
In the more technically advanced diesel systems (i.e. EPIC, DPCN), the nozzle holder acts as a sensor for measuring the injection flow rate and sends this information back to the electronically controlled pumps.
Grinding with Centerless Grinding Wheels
Directly secured to the engine cylinder head, the injector introduces fuel into the engine in the best form for optimum combustion. This requires the breaking down of fuel into tiny droplets, ranging in size from twenty to one hundred microns diameter, and spreading the droplets evenly through the combustion chamber. The injector consists of the nozzle-holder and the nozzle, with the nozzle having to close rapidly at the end of the injection in order to prevent the combustion gases forcing their way up into the injector.
In the more technically advanced diesel systems (i.e. EPIC, DPCN), the nozzle holder acts as a sensor for measuring the injection flow rate and sends this information back to the electronically controlled pumps.

.png)
Engine Valve Grinding with Diamond Rotary Dresser
Diamond rotary dresser for profiling wheels, with diamond grains positioned for dressing and profiling wheels vitrified or resin grinding oblique in-feed grinding for the various stages of the grinding wheel with high precision binder.
Features:
-High consistency:
The rectangular shape of the diamonds is good for wear tolerance, making consistent dressing possible with minimal variation due to edge wear.
-Higher-quality machined goods:
Thanks to improved precision in shaping wheels, superior dimension accuracy, surface roughness and roundness can be obtained.
-Lower grinding costs:
Rectangular diamonds provide superior longevity to natural diamonds, making it possible to reduce grinding costs.
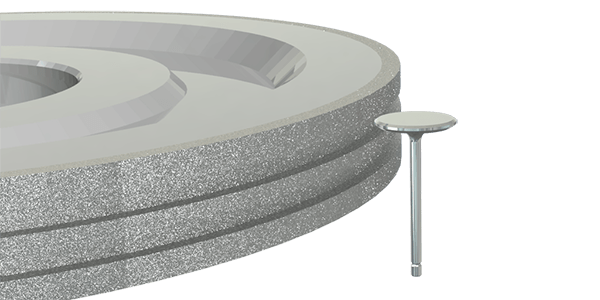
Hydraulic Valve Lifters/Hydraulic Tappets
Hydraulic tappet is a device for maintaining zero valve clearance in an internal combustion engine. Conventional solid valve lifters require regular adjusting to maintain a small clearance between the valve and its rocker or cam follower. Pressurized oil enters through a hole in the lifter body and flows into a narrow channel. This oil enters the internal lifter cylinder but flows freely out the other side. When the cam presses down on the lifter piston, it closes the channel.
Grinding with Vitrified CBN Internal Grinding Wheels
.png)
Piston Ring
A piston ring is a metallic split ring that is attached to the outer diameter of a piston in an internal combustion engine or steam engine.
The main functions of piston rings in engines are sealing the combustion chamber so that there is minimal loss of gases to the crank case, improving heat transfer from the piston to the cylinder wall, maintaining the proper quantity of the oil between the piston and the cylinder wall, and regulating engine oil consumption by scraping oil from the cylinder walls back to the sump. Most piston rings are made from cast iron or steel.
Grinding with Electroplated Diamond Grinding Wheels
Electroplated wheels are noted for relatively large grit protrusion and higher abrasive concentration. This results in very free cutting properties and in high stock removal capacity. Besides, these tools are noted for allowing special shapes and profile tools to be made at short notice and causing very little change on wheel shape after used, suitable for precision grinding.
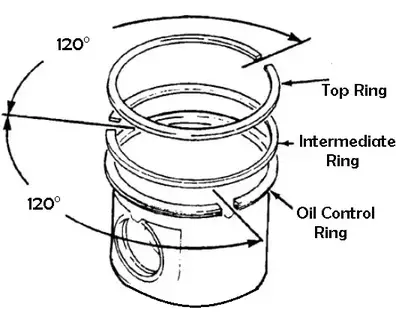
.png)
Gear
Gears, in a car, transmit power from the crankshaft (the rotating axle that takes power from the engine) to the driveshaft running under the car that ultimately powers the wheels. You can have any number of gears connected together and they can be in different shapes and sizes.
Grinding Solutions:
1. Gear angular grinding with Vitrified CBN grinding wheels
Moresuperhard vitrified CBN (Cubic Boron Nitride) grinding wheels are specially used for gear hob cutter grinding. CBN (Cubic Boron Nitride) due to its hardness, thermal resistance which is higher than diamond's, allowing work at 1,900°C (3,500°F), and the good chemical resistance of CBN to ferrous alloys. The roughness and sharpness is the most important for the CBN wheels.
.jpg)
2. Gear internal grinding with Vitrified CBN internal grinding wheels
_.jpg)
.png)
3. Worm gear grinding wheels
The worm grinding wheel is mainly used for grinding the worm gear and worm gear surface of the reducer. The product has good stability, high grinding accuracy and small cumulative pitch error.
It can maintain continuous involute and helical gear geometry. It has good transmission stability and low transmission noise.
.jpg)
Bearing
Bearings are mechanical assemblies that consist of rolling elements and usually inner and outer races which are used for rotating or linear shaft applications, and there are several different types of bearings, including ball and roller bearings, linear bearings, as well as mounted versions that may use either rolling.
Grinding Solutions:
1. internal diameter 2. inner race 3. outer race 4. lip 5. ring face
Grinding with Vitrified CBN grinding wheels
Mainly used for machining cast iron (alloy cast iron, chilled cast iron, nodular cast iron, etc.), steel(45#,55#, 20Cr, etc.)
Features
-Highest speed reach 160m/s
-High precision control standard
-Main performance reach the international advanced level
-Grinding wheels can match with various substrate
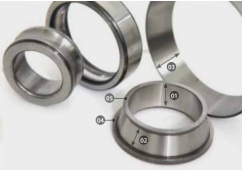
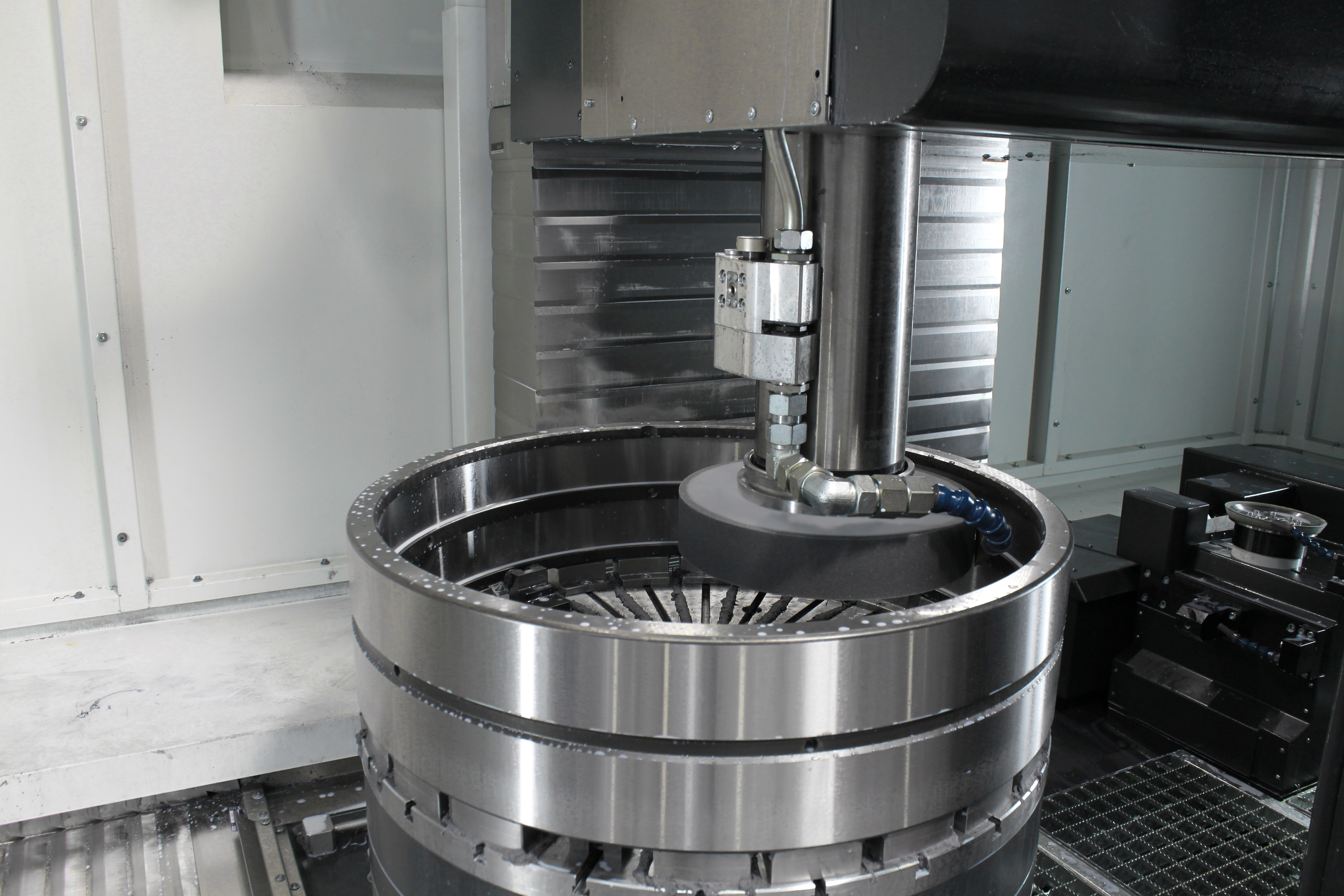
Ball bearing grinding with Rotary Dresser
Rough grinding operations which are carried out by vitrified wheels to remove large amounts of material. Finishing or lapping operations which are carried out by resin wheels to provide a good surface finish.
Vitrified bond/ resin bond grinding wheel is suitable for all kinds of bearing steel ball, carbon steel, stainless steel balls grinding.
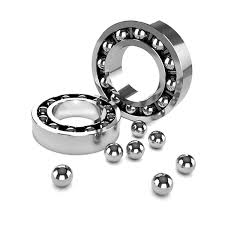
Bearing Face Grinding with Double Disc Surface Grinding Wheel
MoresuperHard company offers a full line of diamond and CBN grinding wheels and dressing stones for fine grinding machines and single and double side lapping systems. Our vitrified diamond and CBN double discs grinding wheels have high grinding efficiency, high wear resistance and abrasive consumption, good surface quality and flatness of the workpiece.
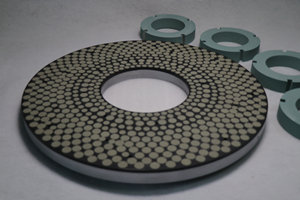
Steering CV joint
Constant velocity, or CV, joints are used to connect your vehicle's transmission to your wheels. CV joints are part of the driveshaft and are used primarily on front-wheel drive vehicles, but they are also used in rear- and four-wheel drive vehicles.
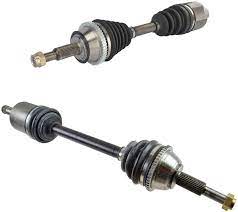
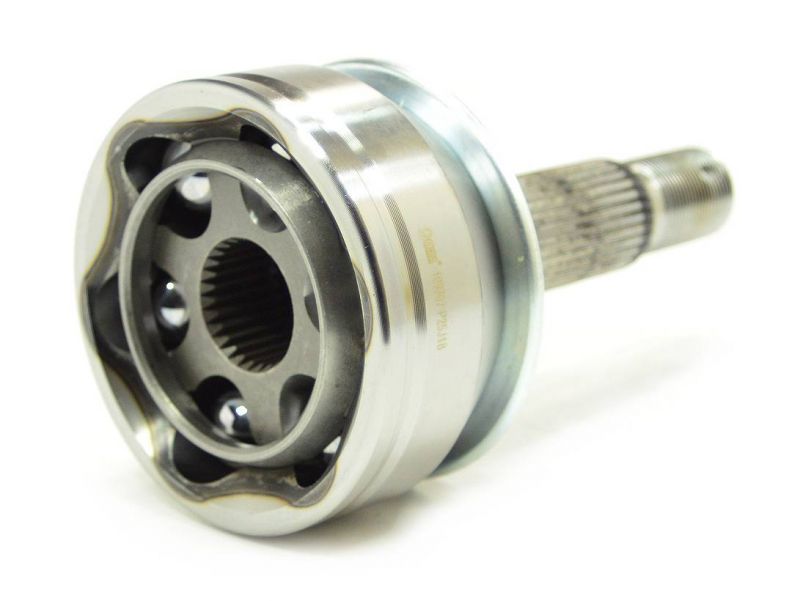
Grinding with Vitrified CBN Internal Grinding Wheels and Rotary Grinding Dressors
Brake and Automobile Wheel Hub Surface
A brake is a mechanical device that inhibits motion by absorbing energy from a moving system. It is used for slowing or stopping a moving vehicle, wheel, axle, or to prevent its motion, most often accomplished by means of friction. Most brakes commonly use friction between two surfaces pressed together to convert the kinetic energy of the moving object into heat, though other methods of energy conversion may be employed. For example, regenerative braking converts much of the energy to electrical energy, which may be stored for later use. Other methods convert kinetic energy into potential energy in such stored forms as pressurized air or pressurized oil.
The hub unit is a device that fills an important role in supporting a car by the wheels, and integrates the bearings and the surrounding components. There is one type of hub unit that rotates smoothly while supporting the vehicle weight, and another type that transmits the driving force from the engine to the wheel.The Hub is the bearing that the wheel is attached to. If you hub is bad, your wheels will vibrate and become loose, which seriously impacts your car's safety and performance.
Brake Pad Grinding with Electroplated Diamond Wheels
Electroplated tools consist in a single layer of superabrasives grains (Diamond or CBN) fixed on the blank by a nickel galvanic process. The thickness of the nickel-coating is always around half of the diameter of the diamond. Electroplated bond grinding wheels are mainly used for machining tungsten carbide, ceramics, glass, composite, sapphire, high speed steel, tool steel, mould steel, stainless steel, cast iron and so on.
.jpg)
Automobile Body
Automotive Safety Glass Edge with Metal Diamond Grinding Wheel
Metal bond Diamond wheels can be used for processing high quality side windows glass, front and back windshield. Rough grinding and fine milling of auto glass.
Usage: Diamond grinding wheels are used for hard carbide, optical glass, gem, semi-conductor materials, non-ferrous materials, and non-metallic material grinding, cutting or electrolytic grinding.

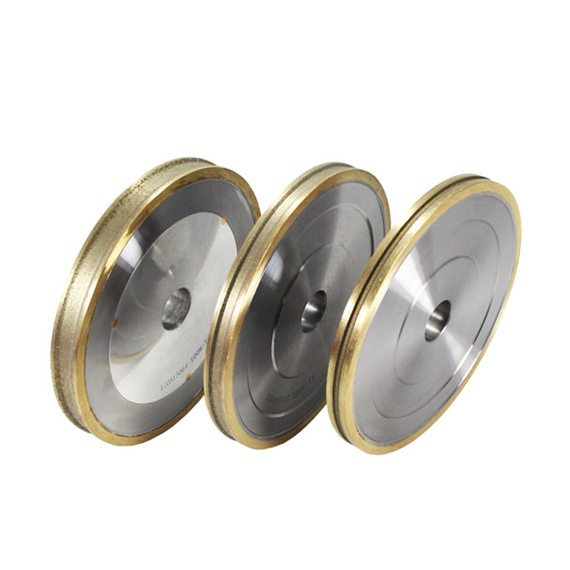