What is Inner Bore of Medical Ceramic Hip?
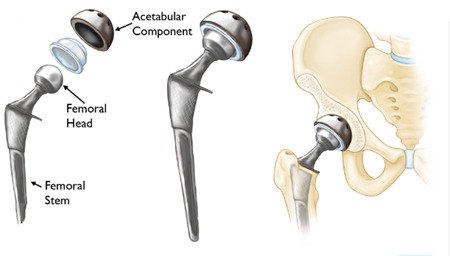
The Inner Bore of Medical Ceramic Hip refers to the hollow space or channel within a ceramic hip implant that is designed to accommodate the patient’s natural femoral head (the ball-shaped top of the thigh bone) during a hip replacement surgery. The inner bore is specially shaped to match the contours of the femoral head and provide a secure fit.
Ceramic hip implants are made from biocompatible materials such as alumina or zirconia. They are known for their excellent durability, resistance to wear, and low friction properties, making them a popular choice for hip replacement surgeries.
What should we pay attention to when we process Inner Bore of Medical Ceramic Hip?
The inner bore of a ceramic hip is carefully engineered to minimize friction and allow smooth movement between the implant and the natural femoral head. This helps to reduce wear and tear on the implant, as well as potentially decrease the risk of complications and improve the overall functionality of the hip joint.
Precision and Accuracy: The Inner Bore must be ground with precision and accuracy to achieve the proper fit and ensure the functionality of the hip implant. Regulations and specifications provided by the manufacturer should be strictly followed to meet the required dimensions and tolerances.
Coolant and Lubrication: Use an appropriate coolant or lubrication system during the grinding process to prevent excessive heat buildup. This helps to avoid thermal damage to the ceramic material and maintain its integrity.
Grinding Parameters: Optimize the grinding parameters, such as wheel speed, feed rate, and depth of cut, to ensure efficient material removal while minimizing the risk of surface damage or overheating.
Quality Assurance: Conduct regular inspections and quality control checks throughout the grinding process. This includes dimensional measurements, surface roughness assessment, and visual inspections to ensure that the Inner Bore meets the specified requirements.
Surface Finish: After grinding, pay attention to achieving the desired surface finish of the Inner Bore. This may involve polishing or additional finishing processes to ensure a smooth, low-friction surface.
Moresuperhard Customer Case of Inner Bore of Medical Ceramic Hip Grinding:
Grinding material:
Inner Bore of Medical Ceramic Hip (oxide ceramics)
Equipment: Composite machining center equipment
The grinding problem that the customer needs to solve:
the experiment is based on the existing equipment conditions, and the inner hole is ground by the combination of turning and milling; the tolerance range is high, the roundness control requirement is 8 microns, and the surface roughness requirement is not high, about 0.8 is enough .
Grinding Solutions: Moresuperhar Electroplated Diamond Grinding Head
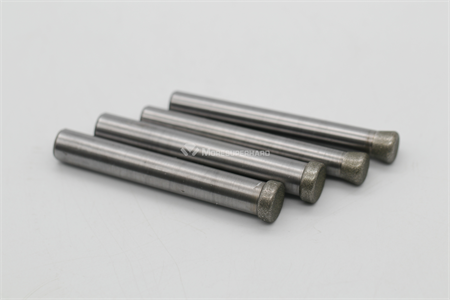
The preliminary plan is set as a high-precision electroplated diamond internal grinding head, with non-standard shape and 2 types of surface design to fit the shape of the inner hole. The overall concentricity is 2 microns, the sand plating is uniform, and the base is made of ordinary alloy rod, which has reached the high-precision standard. The reason for recommending electroplating is that the customer’s equipment is not particularly friendly to trimming support, and needs to be refitted, so as to improve efficiency and reduce costs for customers with the feature of electroplating without trimming.
Customer feedback of Electroplated Diamond Grinding Head:
At present, the overall tolerance accuracy is perfectly grasped, and the grinding efficiency and surface quality are qualified; but the roundness control is not up to standard, the customer requires 8 microns, and the actual test is in the range of 12-15 microns. The preliminary analysis of the problem is as follows: 1. The equipment itself is not a special grinding machine; 2. The rigidity of the base of the grinding head is not enough, and the base material needs to be improved to increase the rigidity;
Improvement of the Moresuperhard grinding solution:
The customer used a 170-mesh
metal diamond grinding head, and used our electroplated grinding head to make a simple finish on the surface, and the actual test results met the requirements. Therefore, we are considering whether it has something to do with the characteristics of the bond, and whether it can achieve the effect by replacing it with a resin or a vitrified bond grinding wheel. The next step is to test two batches of internal grinding heads with different bonding agents, and provide customers with better grinding solutions based on the test results. Grinding material: medical ceramic tube joint inner hole (oxide ceramics).
---EDITOR: Wind Niu,Jackie Wang
---POST: Jackie Wang