Titanium alloy is an alloy with Ti as the main component, and contains aluminum, vanadium, iron, manganese and other elements to improve its performance. Titanium alloys can be divided into α Titanium alloy β Titanium alloys and α–β Titanium alloy. among α–β Titanium alloys (such as Ti – 6Al – 4V) have good comprehensive properties and are most widely used.
Titanium alloy characteristics:
Titanium alloy is considered as a typical representative of "light weight, high strength and heat resistance" materials. Its strength is higher than that of steel, but its density is only about 60%. It can be used in the temperature environment of 300~350 ℃ for a long time. In addition, different types of titanium alloys show technological characteristics in forming and welding, which makes titanium alloys widely used in engineering fields.
Applications of Titanium alloy :
The most representative is in the aerospace field:
the fan blades of aeroengines and the blades/impellers/bladed discs/casings of low-pressure compressors/some high-pressure compressors, the fuel storage tanks of aerospace vehicles, rocket engine casings and other important parts are mostly made of titanium alloys. In the automotive industry, engine valves/connecting rods and exhaust systems made of titanium alloys are of great significance for body weight reduction and engine noise reduction. Thanks to its outstanding biocompatibility, titanium alloys have also become the preferred metal materials for human implants and bone repair.
However, due to the characteristics of high strength, low thermal conductivity and high chemical activity, titanium alloys are difficult to machine, facing low machining efficiency, rapid tool wear, poor machining quality and other problems. Chinese and foreign scholars have carried out a series of studies on this, and discussed the grinding characteristics of titanium alloys under various typical process conditions and the application effects of various tools. Through these studies, we can basically form a more comprehensive and in-depth understanding of the cutting/grinding characteristics of titanium alloys. In this paper, the research progress of grinding titanium alloys will be analyzed in combination with the above aspects.
Main problems in grinding of Titanium alloy:
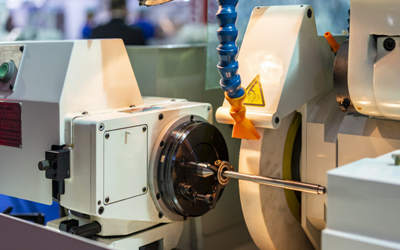
1. High grinding temperature.
Titanium alloy has high strength and good thermal strength, so it will generate a lot of heat during grinding. However, the thermal conductivity of titanium alloys (below 7W/(m · K)) is much lower than that of steel and aluminum alloys; In the grinding process, except that part of the heat can be transmitted through the wear debris, cutting fluid and abrasive tools, only a few of the remaining heat can be transmitted to the workpiece in time, resulting in a large amount of grinding heat accumulating in the contact area. On the one hand, it speeds up tool wear, on the other hand, it thickens the heat affected layer on the surface of the workpiece and reduces the mechanical properties of the part. Sometimes it is necessary to reduce the processing efficiency to reduce the adverse effect of accumulated heat.
2. The elastic deformation of the workpiece material is large.
The elastic modulus of titanium alloy is low, so the elastic deformation is large in the grinding process, which restricts the machining accuracy, especially for thin-walled parts. In addition, the elastic deformation and recovery of workpiece material are important inducements of cutting vibration. If the elastic deformation of the workpiece material is large, the contact area between the workpiece material and the abrasive particles will increase, which will lead to serious wear of the rear cutter face of the abrasive particles.
3. The tool adhesion is serious.
Titanium alloy has good plasticity. Under the action of contact pressure, the cutting edge and workpiece material are easy to produce "cold welding", which causes workpiece material adhesion. In addition, titanium alloys have high chemical activity. Titanium is easy to react with elements such as carbon and nitrogen in tool materials and oxygen in air under the effect of grinding temperature, which increases the adhesion tendency between tools and workpiece materials. The adherent workpiece material will cause a small amount of abrasive materials to fall off together when peeling. The serious adhesion phenomenon is one of the main reasons for rapid tool wear when grinding titanium alloys.
Abrasive selection:
With high hardness, heat resistance, thermal stability, chemical stability, also need some toughness, can withstand a grinding force.
Conventional grinding wheels:
Green silicon carbide abrasives: hard, brittle, with sharp cutting edges, most suitable for titanium alloy grinding
Corundum abrasives: high toughness and hardness, high temperature resistance, high grinding efficiency, mostly brown and white corundum
Superhard grinding wheels:
High hardness, good wear resistance, large thermal conductivity, high efficiency in grinding titanium alloy, diamond grinding wheels are better than CBN grinding wheels in grinding titanium alloy
Vitrified bond can be used for grinding titanium alloy, which has good thermal and chemical stability, low wear and long service life, with the disadvantage that it is brittle and cannot be subjected to large impact and bending.
For cutting and rough grinding, resin bonding and resin bonding can also be used, with the disadvantage of poor thermal stability, easy to burn, and the need for adequate cooling during grinding.